学术论文丨熔盐处理对 SiC 陶瓷表面及其与 Si 涂层界面性能影响研究
2376
2022-01-24 14:22:15
熔盐处理对SiC陶瓷表面及其与Si涂层界面性能影响研究田劲,牛亚然,侯清宇,钟鑫,黄贞益,郑学斌安徽工业大学,冶金工程学院;中国科学院上海硅酸盐研究所摘要:环境障涂层体系中粘结层与基体的结合性能是评价其质量的重要指标之一。
熔盐处理对 SiC 陶瓷表面及其与 Si 涂层界面性能影响研究
田劲 , 牛亚然 , 侯清宇, 钟鑫, 黄贞益, 郑学斌
安徽工业大学, 冶金工程学院;
中国科学院上海硅酸盐研究所
摘要:环境障涂层体系中粘结层与基体的结合性能是评价其质量的重要指标之一。本文针对环境障涂层中硅粘结层与硅基陶瓷材料结合性能不理想的问题, 采用 Na2CO3 和 Na2SO4 熔盐作为蚀刻剂对 SiC 陶瓷表面进行粗糙化处理, 研究了 SiC 陶瓷表面熔盐处理后的显微形貌、 粗糙度以及物相组成。采用真空等离子喷涂技术制备了 Si 涂层,采用划痕法、 压痕法以及拉伸结合强度测试法表征了涂层 - 基体界面的性能, 发现采用高温熔盐处理方法可以显著提高 Si 涂层与 SiC 陶瓷之间的界面结合性能。本工作初步验证了高温熔盐处理方法是一种有效的陶瓷表面粗糙化处理技术。
硅基陶瓷材料, 如 SiC、 C/SiC、 SiC/SiC 等,具有密度低、 耐高温、 力学性能优异等特点, 有望替代高温合金, 应用于航空发动机热端部件。然而, 环境障涂层 (Environmental barrier coating,EBC) 体系的 Si 粘结层与基体之间的结合是其薄弱环节, 将会严重影响 EBC 的服役寿命, 导致基体材料的力学性能显著下降。
涂层与基体的结合强度是评价涂层质量和可靠性的重要指标之一 。影响涂层与基体结合强度的因素较多, 其中基体表面预处理状态是重要的影响因素之一。基体表面处理有多种方法,包括喷砂处理、 高温熔盐处理、 激光刻蚀、 砂纸打磨、 酸洗、 磷化等。其中应用最为广泛的为喷砂处理, 然而相比金属基体, SiC 陶瓷硬度极高,使用喷砂方法易造成表面粗糙度不均匀,影响涂层 - 基体的界面性能。
熔盐处理是在基体表面涂覆一定浓度的蚀刻剂, 然后将试样放入高温环境保温一定时间,然后酸浸泡以去除表面腐蚀产物的表面处理技术。熔盐处理方法能活化基体表面, 增加基体表面粗糙度,并且具有工艺简单、 操作简便、成本低等特点 。孙荆等人研究了 SiC 陶瓷在 Na2CO3 熔盐中 1000℃ 条件下的腐蚀特性, 发现腐蚀主要发生在晶界和晶粒表面的缺陷处, 同时随时间延长, SiC 晶粒本身也被腐蚀, SiC 晶粒表面变得相对光滑, 出现了一些沟槽;腐蚀产物除玻璃态 Na2SiO3 外, 还有结晶型 Na2Si2O5、SiO2 及少量的 SiO。W. C. Say 等人研究了 SiC陶瓷在 Na2SO4 熔盐中的腐蚀动力学行为, 发现在 900℃ 时, 腐蚀速率相对较慢, 可能因为接近Na2SO4 的熔点 (884℃ ) 的原因, 在 900~1300℃温度范围内, SiC 的腐蚀速率随温度升高而增加。N.S. Jacobson 等人研究了 SiC 陶瓷在 1000℃的Na2SO4 和 Na2CO3 熔盐环境的热腐蚀行为, 发现腐蚀 48 h 导致形成的 SiO2 的含量比腐蚀前增加了 10-20 倍, 另外, 还形成少量的 Na2SiO3。SiC陶瓷受 Na2SO4 熔盐腐蚀后表面发生均匀的点蚀;SiC 陶瓷受 Na2CO3 熔盐腐蚀后表面出现局部点蚀和晶界腐蚀。然而, 据文献调研, 未见高温熔盐处理 SiC 陶瓷的表面特性对涂层界面结合性能的研究报道。
本工作简化了环境障涂层体系, 使用 SiC 陶瓷模拟陶瓷基复合材料, 分别采用 Na2CO3 和Na2SO4 熔盐对 SiC 陶瓷表面进行处理, 研究了SiC 陶瓷处理后的显微结构特征, 然后采用真空等离子喷涂技术在处理后的 SiC 陶瓷表面沉积 Si涂层, 采用划痕法和压痕法测定和观察涂层与基体的划痕形貌、 压痕形貌和裂纹扩展形式, 采用拉伸法测量涂层与基体的结合强度, 观察涂层与基体的拉伸断裂面。本工作证明了高温熔盐方法是一种有效的 SiC 陶瓷表面粗糙化方法, 可以有效提高涂层 - 基体的界面结合性能。 采用反应烧结碳化硅 (reaction sintered silicon carbide) 作 为 基体材料,尺寸为Φ25.4 mm ×5.0mm。采用 Na2CO3 和 Na2SO4 熔盐作为刻蚀剂。为了使熔盐能够均匀地铺展在 SiC 表面,配置了浓度为 10wt.% 的 Na2CO3 和 Na2SO4 溶液。具体步骤为,使用胶头滴管在 SiC 基体表面涂覆一层蚀刻剂,将样品放入烘箱中烘干, 然后放入马弗炉中进行熔盐处理,以 10℃ /min 的升温速率升至900℃,保温 4 h,之后随炉冷却。取出冷却的样品,将其放在氢氟酸中进行超声波震荡,并用蒸馏水冲洗干净,放入烘箱内烘干,取出备用。采用真空等离子喷涂技术(Vacuum Plasma Spray, VPS, A-2000, Sulzer Metco AG, Switzerland)在熔盐处理后的 SiC 陶瓷表面沉积 Si 涂层,厚度约 18~200 μm,喷涂工艺见本实验室之前报道。
采用 X 射线衍射仪(RAX-10 型,Rigaku 公司,日本) 对熔盐处理样品表面的物相组成进行分析,选用 Cu Kα 射线 (λ = 0.15406 nm),工作电压和电流分别为40 kV 和100 mA,2θ 扫描范围为 10~80°,扫描速率为 5° /min。采用场发射扫描电子显微镜(S-4800 型, Hitachi 公司,日本)观察样品的表面、截面和断面显微形貌, 采用配带的 EDS 能谱仪进行成分分析。
采用数字式显微硬度计(HXD-1000 TMC/LCD,上海泰明光学仪器有限公司,中国)在涂层 - 基体界面处进行压痕实验, 实验条件为:试验载荷为 500 gf, 保载时间为 10 s。采用多功能材料表面性能试验仪(MFT-4000 型,中国科学院兰州化学物理研究所, 中国) 进行划痕实验,实验条件为:锥角120°的 Rockwell C 金刚石压头,压头顶端为曲率半径 R=200 μm 的球形,0~100N 均匀地施加恒定正压力,其中每次的正压力间隔值为10 N, 划痕长度 d=5 mm,划痕时间为 60s。根据 GB/T 8642 标准《热喷涂层结合强度的测定》,使用材料万能试验机 (Instron 5592,美国)采用拉伸法测量涂层 - 基体界面结合强度。
图 1 为 未 处 理 的 SiC 陶 瓷 及 其 Na2CO3 和Na2SO4 熔盐 900℃ 处理 4 h 的 SiC 陶瓷表面微观形貌。从低倍形貌(图 1(a), 1(b) 和 1(c)) 可以看出,经两种熔盐腐蚀后, SiC 陶瓷表面粗糙程度增加。其中, 未处理的碳化硅的表面粗糙度 Ra 为0.51± 0.22μm, Rmax 为 1.20± 1.45 μm;Na2CO3熔 盐 腐 蚀 试 样 的 表 面 粗 糙 度 Ra 为 2.34± 0.44μm, Rmax 为 16.98±12.16 μm;Na2SO4 熔盐腐蚀试样的表面粗糙度 Ra 为 2.85± 0.81 μm, Rmax为 20.79± 10.03 μm, 从高倍形貌( 图 1(d), 1(e)和 1(f)) 可以看出, 两种熔盐腐蚀样品晶界处的腐蚀现象均显著, 导致 SiC 晶粒凸起, SiC 晶粒尺寸比较接近, 约为 15~25 μm。值得注意的是,虽然 Na2CO3 熔盐腐蚀样品的 Ra 和 Rmax 小于Na2SO4 熔盐腐蚀样品, 其形成的 SiC 晶粒表面较粗糙, 且晶界处的孔洞较明显;而 Na2SO4 熔盐腐蚀样品的 SiC 晶粒表面较平滑, 且晶界处的孔洞较少。
图 1 SiC 陶瓷表面微观形貌:(a), (d) 未处理的 SiC 陶瓷;(b), (e) Na2CO3 熔盐 900℃处理 4 h;(c), (f) Na2SO4 熔盐 900℃处理 4 h
图 2 为在 900℃ Na2CO3 和 Na2SO4 熔盐中处理 4 h 的 SiC 陶瓷的 XRD 图谱。可以看出, 两种熔盐腐蚀后, SiC 陶瓷的相组成是相同的, 主要是由 SiC 和 Si 以及少量 Na2Si2O5 组成。其中,Na2SO4 熔盐腐蚀样品的硅含量明显多于 Na2CO3熔盐腐蚀样品的硅含量。SiC 陶瓷中的 Si 相主要来源于其制备过程中填充到孔隙的游离硅 。熔盐腐蚀过程中, 可能发生的化学反应包括:
(1) 在 Na2CO3 熔盐腐蚀条件下,
(2) 在Na2SO4熔盐腐蚀条件下,
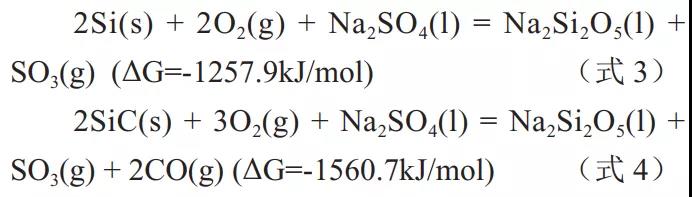
从式 1-4 可以看出,在腐蚀过程中,陶瓷中的 SiC 和 Si 相均可以与 Na2CO3 和 Na2SO4 熔盐发生化学反应。从在反应温度的吉布斯自由能 (ΔG)比较可以发现, Na2SO4 更容易对 SiC 和 Si 相造成腐蚀, 使得试样表面的粗糙度相对较大。刻蚀后SiC 陶瓷表面存在 Na2Si2O5 等杂质相, 可能降低硅涂层与基体的结合强度。因此, 在喷涂前将经熔盐腐蚀的试样放在 20% 氢氟酸中进行超声波震荡除去盐层,并用蒸馏水冲洗干净, 放入烘箱内烘干处理, 然后进行喷涂实验。
图 3 为 Si 涂层的截面形貌和涂层 - 基体的界面形貌。从低倍形貌(图3(a) 和 3(b))可以看出,Si 涂层较为致密,与 SiC 陶瓷界面结合紧密。从高倍形貌(图 3(c) 和 3(d))可以看出,经 Na2CO3熔盐腐蚀试样的基体-涂层界面处存在较多的孔洞,而 Na2SO4 熔盐腐蚀试样基体 - 涂层界面缺陷较少。
图 2 Na2CO3 和 Na2SO4 熔盐 900℃处理 4 h 的 SiC 陶瓷表面 XRD 图谱
图 3 SiC 陶瓷表面 Si 涂层截面形貌:(a), (c) Na2CO3 熔盐 900℃处理 4 h;(b), (d) Na2SO4 熔盐 900℃处理 4 h
为了进一步验证涂层 - 基体间的界面结合性能, 考察涂层 - 基体界面的划痕性能、 压痕性能和拉伸结合性能。图 4 为在 900℃ 熔盐中处理 4h 的 SiC 陶瓷表面制备的 Si 涂层的划痕形貌。进行划痕实验前, 用细砂纸把涂层磨薄至 20~50μm,以观察界面结合性。从低倍形貌( 图 4(a)和 4(b))可以看出,Na2CO3 熔盐处理的 Si 涂层划痕形貌较深, 并且划痕处涂层剥落现象明显;而 Na2SO4 熔盐腐蚀试样的划痕深度较浅,未见划痕处有明显的涂层剥落现象。从高倍形貌(图4(c) 和4(d))可以看出, Na2CO3 熔盐腐蚀试样的涂层碎裂现象明显,在划痕处存在大量的碎屑,而 Na2SO4 熔盐腐蚀试样的内部颗粒呈现阶梯状碎裂, 且未发现明显的碎屑分布在划痕处。
图 4 SiC 陶瓷表面涂层 - 基体界面处的划痕形貌:
(a), (c) Na2CO3 熔盐 900℃处理 4 h; (b), (d) Na2SO4 熔盐 900℃处理 4 h
图 5 为在 900℃熔盐中处理 4 h 的 SiC 陶瓷表面制备的 Si 涂层与基体界面处的压痕形貌。从图5(a) 可以看出, 经 Na2CO3 熔盐腐蚀试样的压痕形貌完整,靠近压痕处的裂纹较明显,同时压痕附近出现了崩落的痕迹,推测此处应力较大。从图5(b) 可以看出,经 Na2SO4 熔盐腐蚀试样的压痕形貌完整,压痕附近的裂纹较细小。
采用拉伸实验表征 Si 涂层与 SiC 陶瓷的拉伸结合强度。发现经 Na2CO3 熔盐腐蚀试样的拉伸结合强度值为 5.95±0.50 MPa,经 Na2SO4 熔盐腐蚀试样的拉伸结合强度值为 8.34± 1.64 MPa,表明Na2SO4 熔盐处理表面更有利于表面 Si 涂层的结合性能。将熔盐处理样品与传统喷砂处理样品进行了比较, 发现经喷砂处理 SiC 陶瓷表面 Si 涂层样品的拉伸结合强度值无数值,因为在进行拉伸实验前, 用手可以将基体与涂层自动分离。这个现象证明, 相对传统喷砂工艺,熔盐处理可以有效提高涂层与 SiC 陶瓷涂层的界面性能。
图 5 SiC 陶瓷的涂层 - 基体界面压痕形貌:(a) Na2CO3 熔盐 900℃处理 4 h;(b) Na2SO4 熔盐 900℃处理 4 h
图 6 为拉伸实验后的 Si 涂层与 SiC 陶瓷基体界面处的宏观断裂形貌。可以发现,两种试样的拉伸断裂均发生在涂层 - 基体界面处,断裂面较平整。图7 为拉伸实验后的 Si 涂层与 SiC 陶瓷基体界面处的微观形貌与 EDS 元素面分布结果。经两种熔盐腐蚀试样的断裂表面均呈现凹凸不平,高倍下可以明显地看到晶粒的形状(基体表面),元素分析进一步证明拉伸断裂处为涂层 - 基体界面。
图 6 SiC 陶瓷表面涂层 - 基体断裂宏观形貌:(a) Na2CO3 熔盐 900℃处理 4 h;(b) Na2SO4 熔盐 900℃处理 4 h
图 7 SiC 陶瓷表面 Si 涂层拉伸试验后 Si 涂层处断裂面的微观形貌与 EDS 元素分析:(a), (c), (e1), (e2) Na2CO3 熔盐 900℃处理 4 h;(b), (d), (f1), (f2) Na2SO4 熔盐 900℃处理 4 h
本文以SiC陶瓷为基体,进行Na2CO3 和Na2SO4 熔盐处理, 研究了熔盐处理对其表面结构的影响,并采用真空等离子喷涂技术在处理的SiC 陶瓷表面沉积 Si 涂层, 研究了涂层 - 基体的界面结合性能,主要结论如下:
(1) 采用 Na2CO3 和 Na2SO4 熔盐在 900℃ 处理 4 h 实验条件下, SiC 陶瓷表面发生显著腐蚀,导致表面粗糙度分别达到 Ra 为 2.34±0.44 μm和 2.85±0.81 μm, Rmax 为 16.98±12.16 μm 和20.79±10.03 μm。
(2) 真空等离子喷涂 Si 涂层与两种熔盐处理的 SiC 陶瓷基体界面结合紧密, 缺陷较少;划痕和压痕实验进一步证明 Si 涂层与 SiC 陶瓷界面结合性能良好。
(3) Si 涂层与 Na2CO3 和 Na2SO4 熔盐处理的SiC 陶瓷基体的拉伸强度分别为 5.95±0.50 MPa和 8.34±1.64 MPa, 显著高于传统喷砂处理。本工作初步证明, 高温熔盐处理是一种有效提高陶瓷表面粗糙化的方法, 有利于提高 EBC 体系中涂层 - 基体界面结合性能。